Sale of furnaces of polycrystalline growth for the realization of silicon ingot for the photovoltaic one - (Manufactured in France)
Realized by a French manufacturer of vacuum furnace with recognized, founded in 1994, based on the co-operation of 3 engineers, having more than 7 years of knowledge in photovoltaic crystallization.
This realization is the fruit of this team which designed this photovoltaic furnace, most compact currently existing on the market.
This smelting furnace is a tool for crystallization for the production of silicon multicristallin ingots of 240 kg and more, up to 300 kg.
A realization innovating required and carried out in order to occupy a minimum of place because of the impressive growth of the die of photovoltaic, but also innovating by its mode of single control of the heat gradient.
Advantages… obtained !
Compact equipment concentrated on the minimal occupied surface (patented).
A technological tool for a peak productivity with an excellent return on investment (placement of capital).
Can be appropriate for an investment plan or for the realization of photovoltaic field.
Simplicity and French quality.
Loading and frontal unloading !
By silicon ingot (crucible) of 240 kg, it is possible to obtain 10624 wafer (solar cell) per ingot :
that is to say an equivalent of 22300 Watts, by ingot.
137 silicon crucibles / year
96% of operation during 329 days
Cycle time per crucible: 55 hours
3056000 Watts (3 megawatts) is the equivalence of 1455000 photovoltaic cells of 2.1 Watts each one,
allowing the realization of 15156 photovoltaic solar panels of 200 Watts / Year, made up each of 96 cells of 2,1 Watts each one.
The following phases after the crystallization of the silicon ingot, consist :
- to make it cut out in wafer.
- to assemble Wafer in photovoltaic solar panel.
(An ingot makes it possible to carry out to 110 solar panels of 200 Watts made up each of 96 cells).
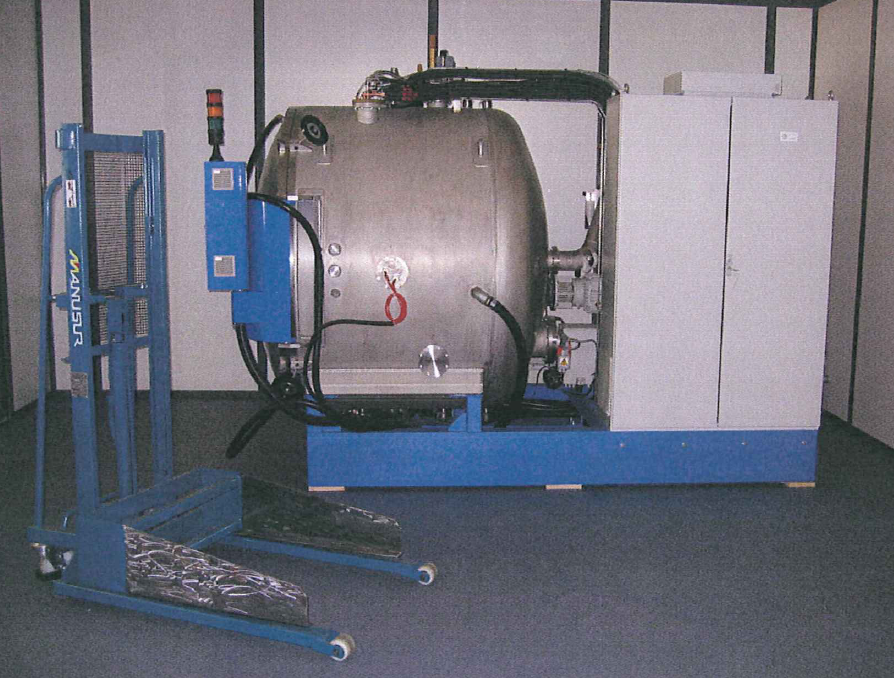
This photovoltaic furnace from its compactness, implies an easy approach of the connection of the fluids.
Dimensions of the photovoltaic furnace (Meter) : Depth 3 x Width 2 x Height 2,5
The process is entirely automated by PLC, and is supervised and controlled by means of computer by an application software developed by the manufacturer.
The software installed was already evaluated on more than 100 models different of furnaces, designed by the same one and single manufacturer.
This software makes it possible to visualize the graphics of the stage of the evolution of the process, to record the data in real-time in a file, as well as the storage of files, being able to be used in particular to make data analyzes.
Optimization of maintenance of this smelting furnace
The modular concept allows the fast replacement of the internal elements in the event of intervention on the various components of the furnace, and a fast visual monitoring.
Ingot usable for the photovoltaic production
Is appropriate for ingot with standard dimensions of 68 cm. x 68 cm. x 25 cm. to make ingot multicristallin of 270 kg silicon.
Cycle time per ingot of polysilicium of 240 kg : less than 50 hours.
Electricity consumption : 150 kVA
Intensity : 170 VA
Three-phase food (without neutral) : 400 V
Frequency 50 Hz
Gas : 2 gases maximum (99.9999%)
Consumption lower than 20 m³
Room with fusion
Stainless steel room with double wall water-cooled of a volume of 3 m³ approximately.
The furnace consists of a cylindrical STAINLESS enclosure, of a diameter of 1,8 meter a 1,5 m depth,
it is put vacuum by a primary pump of a capacity of 300 m³/hr and of a ROOTS of 1000 m³/hr.
This enclosure constitutes the principal room of fusion, comprising :
- a double wall water-cooled
- a manual door of loading
- a “casing” insulated inside, the interior of the enclosure is equipped with a manual door.
This casing integrates resistances of heating out of graphite partly higher, a power of 100 kw,
and resistances partly lower of a power of 50 kW.
That is to say a total of 150 kW.
The lower part comprises 2 actuated shutters each one by a motor bike reducer.
It is the photovoltaic furnace most compact of its generation.
It is advantageous by its simplicity, its automatism and it is equipped with multiple points of safety for the user.
Dimensions of the silicon ingots
Its volume and its zone of load make it possible to accommodate an ingot (silica crucible) of 240 kg to dimensions in centimetre : 72 Length x 72 Width x 40 height
Maximum load capacity: up to 300 kg (240 kg of silicon and 300 kg with the crucible).
The entire surface from site to be envisaged, closed furnace, 2,1 meter X 3,5 meter is lower than 7,5 square meter.
Total height of the equipment : 2,45 meter.
Total mass of the equipment in the course of application : 5000 kg (5 tons).
Volumetric and thermal characteristics
Cooling with water :
During the stage of fusion : 150 liters / minute
During the stage of solidification : 150 liters / minute
Pressure of use : 3 bars
Cooling of the temperature by water provision: 25°C maximum
Compressed-air system
Minimal pressure of power supply of the electromagnetic sluice gates : 6 bars minimum, 10 bars maximum
Consumption by cycle : ~2 N.m ³
System of loading / unloading of the silicon ingot
The procedure of loading/unloading is carried out by a specific loader, adapted as shown on the photographs present.
Impossibility of the risk of overflow of the silicon ingot in the course of fusion
This patent was deposited by the manufacturer of this photovoltaic furnace.
It even makes it possible to use silicon ingots “having been missed”.
We could produce ingots without problem and any incident.
The concept of this photovoltaic furnace as realized by its manufacturer is that in the case of overflow or of rupture of the crucible, silicon in fusion does not have any other possibility but of remaining within a partly cold limit, enabling him to crystallize.
Impossibility of thermal risk of explosion
The risk of explosion is always existing in the furnaces of production of silicon ingot.
This arrives when there is a rupture of the crucible causing a flow of molten silicon reaching a wall of the furnace, the latter being doubled for the passage of the coolant circuit to water.
The explosion arrives by thermal shock occurring between silicon in fusion and the metal wall inside which the water circuit playing passes its part of cooling.
This phenomenon starts also a great quantity of steam, but can also oxidize part of beforehand molten silicon, causing a pressure so strong which it is higher than the bearable limits of the photovoltaic furnace.
Here how the explosion of a photovoltaic furnace occurs.
This type of risk of explosion is impossible with this photovoltaic furnace because of its design which has a site entirely containing the ingot of silica and preventing it in this direction of this risk of molten silicon overflow.
The whole of silicon being entirely contained in its site without possibility of overflow.
Moreover, this photovoltaic furnace is equipped,
- of a warning device in the event of risk of too high pressure,
- of oversize anti-explosion valve compared to the standard.
Impossibility of the risk of flood
In the event of steam making its appearance, water runs out by the lower part of the furnace.
Water cannot thus stagnate indefinitely, it evacuates by the bottom of the furnace, moreover, the high temperature of the furnace puts an end to the appearance of the steam has just been evacuated.
Information of the manufacturer
Start date of manufacture : 2008
Go back to marketing in a new state : - Nothing -
Cut-over date in the establishment : - Nothing -
Condition of startup : - Last nines -
Place of control: NC (France)
Realizable manufacture in several specimens
Our form present at the foot of the page enables you to transmit to the manufacturer, your request for price, according to the number of desired specimen.
Energies and products implemented
Electrical energy : 3 phases without neutral
Diagram : IT
Power circuit : 400 V - 50 Hz - 150 kW
Control circuit : 24 Vcc
Cooling water circuit : 9 m3/h
Pressure on furnace : 3 bars
Maximum temperature : 25 °C
Hydraulic power : - Nothing -
Thermal energy : Furnace
Nature : Graphite resistances
Power : 100 kW + 50 kW
Temperature : 1550°C maximum
Matters and products used
Water : For the cooling of the furnace
Flammable products : - None -
Acids and bases : - None -
Toxic products : - None -
Other matters : Silicon to be melted (Polycrystalline / Monocrystalline)
Components
A gas supply Argon.
2 transformers of heating 400/39 V - 100 kW and 400/20 V - 50 kW
1 electrical equipment box
1 control panel fixed on the furnace and directional
Mode ON
The furnace comprises the 2 following operating processes :
In automatic mode, the operator starting from the supervision, selects a sequence then the order.
In manual mode, the operator starting from the supervision, selects a function then the order.
Modes of STOP
The stopping of the furnace is ordered starting from the supervision or by pressing the pushbutton GENERAL STOP.
User of the photovoltaic furnace (operator)
Only one operator works on the smelting furnace.
The operator carries out the operation of loading of the silicone crucible using a specific industrial truck.
The operator orders the furnace, the process of fusion, the process of crystallization.
The operator carries out the operation of unloading once the finished cycle.
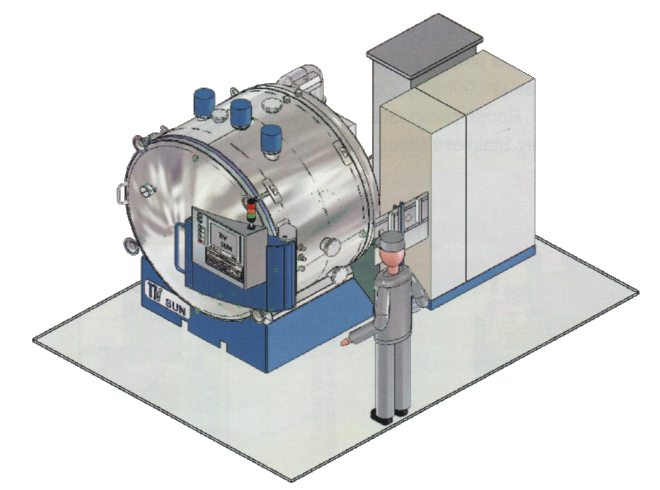
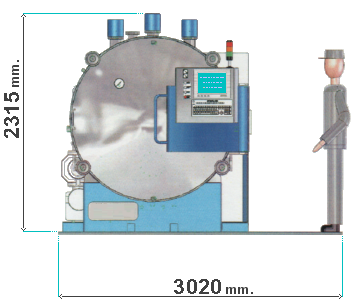
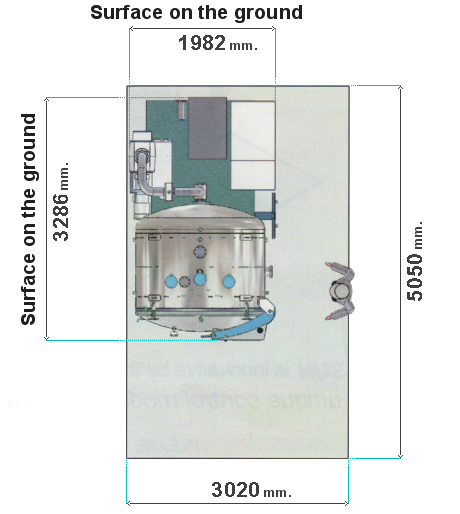